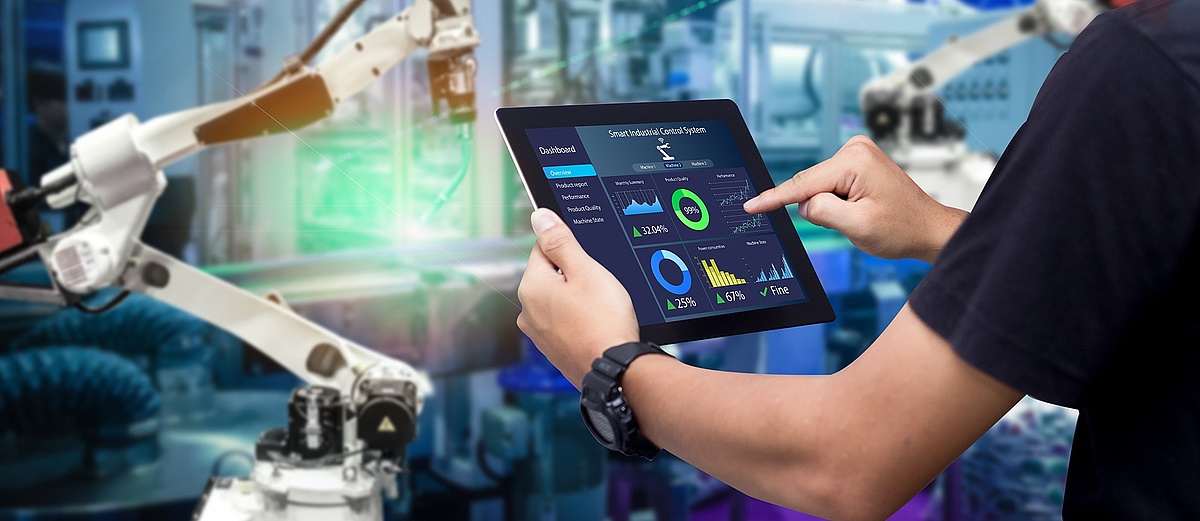
Chancen und Herausforderungen der Industrie 4.0
Industrie 4.0 ist in den letzten Jahren zu einer Art Buzzword geworden – etwas unfair eigentlich, denn das dahinterstehende Konzept ist weit mehr als nur eine Mode oder ein Trend. Stattdessen ist es eine dringend benötigte Möglichkeit, die Produktivität im produzierenden Gewerbe zu verbessern. Kurz gesagt ermöglicht die vernetzte Produktion nach dem Konzept der Industrie 4.0 den schnellen, automatischen Datenaustausch entlang der gesamten Wertschöpfungskette.
Im Vergleich zur „klassischen“ industriellen Produktion ergeben sich daraus eine Reihe von Vorteilen:
- Mit den gewonnenen Daten lassen sich einzelne Prozesse und Prozessschritte noch besser aufeinander abstimmen und so z. B. Leerlauf vermeiden oder auf ein Minimum reduzieren, wodurch die Leistung insgesamt gesteigert wird.
- Auch die Lagerhaltung kann auf diese Weise effizienter werden: ERP Systeme erfassen kontinuierlich Bestandszahlen und ordern automatisiert Nachschub, so dass insgesamt weniger Lagerplatz benötigt wird.
- Im Detail kann auch die Vernetzung einzelner Maschinen und Devices untereinander die Potentiale der Produktionseinrichtung wesentlich erhöhen.
- Dazu zählt auch die deutlich schnellere Identifikation von Fehlerursachen durch die Vernetzung mit integrierten Sensoren.
- Auf Basis der gesammelten Daten können Störungen und so ungeplante Downtime vermieden werden.
Natürlich bringen die neuen Chancen der Industrie 4.0 auch neue Herausforderungen mit sich:
- Die Vernetzung der Maschinen miteinander oder gar der Außenwelt erhöht das Risiko von Cyberangriffen. Neben Sabotage und unerkannten Qualitätsproblemen steigt damit auch das Risiko von Spionage und dem Verlust von Intellektuellem Eigentum. Zusätzlich zu den finanziellen Folgekosten droht damit auch ein wesentlicher Reputationsverlust.
- Die Vernetzung bedingt außerdem, dass insgesamt mehr Endgeräte und Verbindungen in der Produktion Einzug halten. Das erhöht die Komplexität in der Infrastruktur und macht es sehr
aufwendig bzw. fast unmöglich, manuell jederzeit aktuelle und akkurate Geräteinformationen über die Hard- und Softwarestände in der Produktionsumgebung zu erfassen und zu pflegen. Einfach
gesagt: Die Fehleranfälligkeit steigt und die Übersichtlichkeit nimmt ab.
Ein Ansatz: Die IEC62443
Um dieser Anfälligkeit gegenüber Cybergefahren zu begegnen, ohne auf die Potentiale der Industrie 4.0 zu verzichten, sind entsprechende Schutzmaßnahmen nötig. Einen Ansatz hierzu gibt z. B. die internationale Normenreihe IEC62443, die mit „Defense in Depth“ eine umfassende Orientierung bietet.
Was ist mit Defense in Depth gemeint?
Das Konzept ist am einfachsten mit einer Ritterburg zu erklären. Diese baut auf voneinander unabhängigen Schutzmechanismen auf: Von außen ist sie zunächst mit einem Graben, gefolgt von einer Burgmauer geschützt. Innerhalb der Mauer ist die Fläche in mehrere Burghöfe segmentiert, die ein Angreifer nacheinander erobern muss. Im Zentrum steht dann die Zitadelle bzw. der Burgfried, in der sich die Verteidiger als Ultima Ratio verschanzen können.
Auf ein Netzwerk übertragen sieht Defense in Depth ebenfalls eine gestaffelte Verteidigung vor, die ein Angreifer der Reihe nach überwinden müsste, um seine Ziele zu erreichen.
- An erster Stelle steht hier der menschliche Faktor: Durch IT-Sicherheitsrichtlinien, kontinuierliche Schulung der Mitarbeiter und Überprüfung von Arbeitsprozessen können bereits viele Schwachstellen eliminiert werden – Stichwort: Awareness für IT-Sicherheit in der Produktion.
- Der nächste Schritt ist die strikte Trennung der Netzwerke zwischen Office IT und der Produktion. So kann verhindert werden, dass Angriffe auf einen Bereich auch automatisch den anderen in Mitleidenschaft ziehen.
- Ein weiteres Element ist die Segmentierung des Netzwerks in kleinere Partitionen. So kann erschwert werden, dass erfolgreiche Eindringlinge automatisch Zugriff auf das gesamte Netzwerk haben.
- Im Kern steht dann eine Absicherung der Endpunkte. Im ersten Schritt muss festgestellt werden, welche Geräte mit welchem Soft- bzw. Firmwarestand in der Produktion überhaupt vorhanden
sind. Mit diesen Inventarisierungsdaten können eventuell vorhandene Schwachstellen identifiziert und eine Risikobewertung vorgenommen werden. Daraus ergibt sich wie die Endgeräte am besten
geschützt werden können: Z. B. durch die Absicherung von Schnittstellen gegen die unerwünschte Verwendung von (kompromittierten) externen (USB-)Datenträgern. Ein System zur Absicherung und
Vorhalten von Daten hilft, Systeme schnell wiederherzustellen. Zudem kann ein Patch Management eingesetzt werden, um ggf. bekannte, kritische Schwachstellen in Applikationen, Betriebssystem
oder Firmware zu schließen.
Niemals ein 100 prozentiger Schutz, aber…
Absolute Sicherheit gibt es nirgends im Leben. Das gilt insbesondere in der Welt des Digitalen. Dennoch ist es sinnvoll, Cyberangreifern das Leben so schwer wie möglich zu machen. Hat man sein System mit Blick auf diese – vergleichsweise einfachen – Sicherheitsmaßnahmen eingerichtet, reduziert sich die Gefahr eines erfolgreichen Angriffs erheblich und machen das Unternehmen zu einem weniger lukrativen Ziel. Insgesamt wird so die Verfügbarkeit der Produktion verbessert und Unternehmen können beruhigter die Chancen und Potentiale der Industrie 4.0 und des Industrial Internet of Things (IIoT) nutzen.